ここ2回の記事で自分が入社1年目の頃に意味を調べていた単語集の機械・電気工学編、機械加工編を紹介しました。今回はその続きでマシニングセンタ編を紹介したいと思います。特に見積や打合せで出てきた単語が初めは全く理解できず話についていけずに苦労しました。
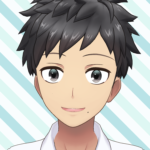
初めは外国語を聞いているんじゃないかと思うほど聞き取ることもできず、正直打合せ中も眠かったのを覚えています。
この記事の目的
・文系出身でこの業界(製造業や機械商社、機械メーカー)に入ったばかりの人が、マシンングセンタの構造や各機能を理解できるように。
・マシンングセンタの見積内容を理解できるように。
・新たにこの業界にきた人に教える方などが、初心者が何にわからなかったのかを理解するために。
※自分の言葉やネットで調べた文章で書いているので正確でない場合があります。
機械・電気工学編はこちら
機械加工編はこちら
マシニングセンタの構造
マシニングセンタとは
ドリルやカッターなどの工具を回転させて金属を削る切削加工機。NC装置で加工内容をプログラミングされ、自動で工具を交換できるATC(自動工具交換装置)により、様々な加工を連続して行うことができる。ワーク(製品)は固定され、工具(ドリルやカッターなど)が回転する。移動は工具を持った主軸側が動くタイプとワークを乗せたテーブルが動くタイプがある。
構造に関してはモノタロウのサイトにわかりやすい記事がありましたのでリンクを貼らせていただきます。
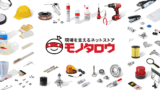
横型と縦型それぞれの特徴
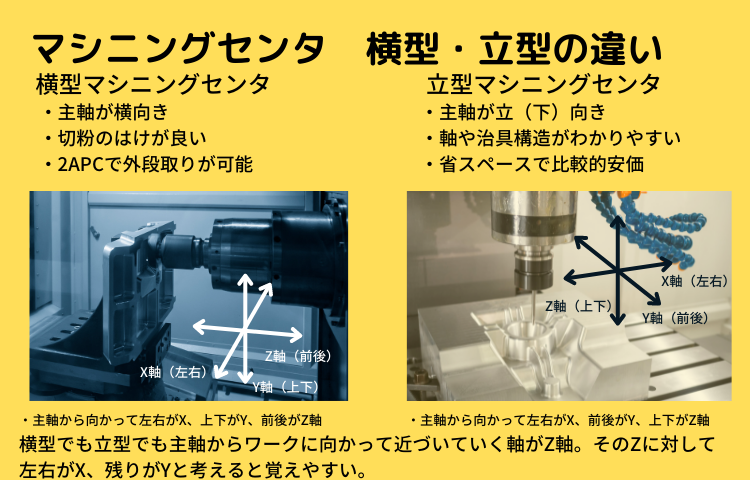
横型マシニングセンタ
主軸が横向き。切粉のはけがよく、2面APC(後述)にすることで、加工中に次のワークを段取りできる。
立型マシニングセンタ
主軸が立向き。上から加工するため軸や治具の構造がわかりやすい。比較的省スペースで低価格。
※横型でも立型でも主軸からワークに向かって近づいていく軸がZ軸。そのZに対して左右がX、残りがYと考えると覚えやすい。
5軸加工機
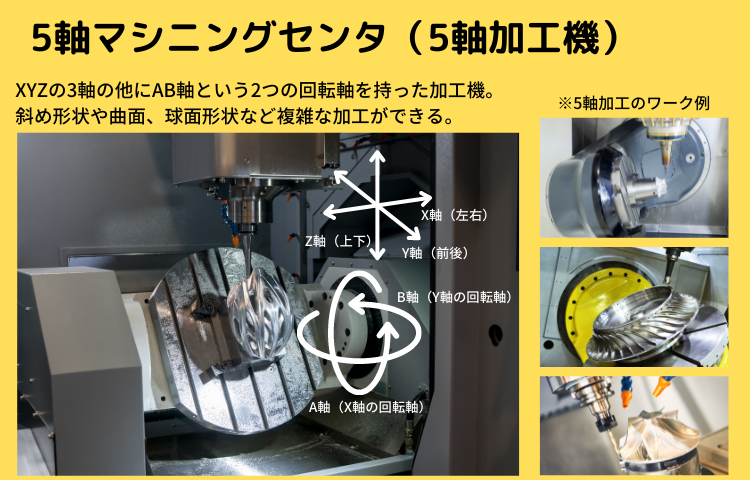
XYZ軸の他に2軸(AB軸)動かせる機械。曲面の加工など、複雑形状の加工を行うことができる。
同時5軸 加工しながら5軸とも同時に動かすことができる機械。複雑な局面などは同時5軸が必要となる。
割出5軸 パレット・テーブルを割出してから加工する機械。加工しながらテーブルを5軸回転できないため、タービンブレードなどの複雑な曲面は加工できない。ワークを付け替えなしで5面加工することに用いられる。
3軸のマシニングセンタ(一般的な横型や立型)にインデックステーブルを乗せて割出5軸のようにすることもあります。
インデックステーブル:割出し(任意の位置で停止)できる回転テーブル。
インデックス(工作機械における):任意の一で停止ができる割り出し機能。NC制御により回転、割り出しを高精度に行える。その機能を持たせた円形のテーブルをインデックステーブルという。インデックステーブルはロータリーテーブルとも呼ばれる。
割り出し 回転軸の角度に対する位置きめ。任意の角度で止めることを割り出しという。
ツールシャンク(BT,BBT,HSK)、マシニングセンタの番手:30番、40番、50番など
主軸のツールを取り付ける部分のテーパの大きさ。BT30,40,50やHSKなどサイズや規格の違いがある。BTとはボルトグリップテーパの略。下記記載のプルスタッドを引っ張って主軸と工具を連結させる方式。
BT30 小型。主軸の設置面積が少なく、重切削には不向き。しかし慣性が少なく、最高回転数に達する時間が短くシンクロタップ加工で高速反転に適している。アルミなどの加工に用いられる。
BT40 中型。BT30ではできないフライス加工や鉄、鋼材の加工に用いられる。
BT50 主軸に装着している面積が広いので重切削向き。
プルスタッド(ボルト)
工具(ホルダ)のテーパシャンクの後ろに取り付けてある突起物。これを主軸が引っ張ることにより工具を保持することができる。
BBT(2面拘束) テーパだけが主軸と接触しているBTと違い、ツールホルダの端面も主軸と接触する2面拘束タイプのホルダ。2面で拘束しているため、テーパ部だけのBTと比べて剛性が高い反面、切粉を噛んで不良品を排出する可能性が高くなるデメリットがある。
HSK テーパの長さが1/10と短く、高速回転することで開いてクランプされる。テーパ部だけでなく、端面も拘束(2面拘束)。
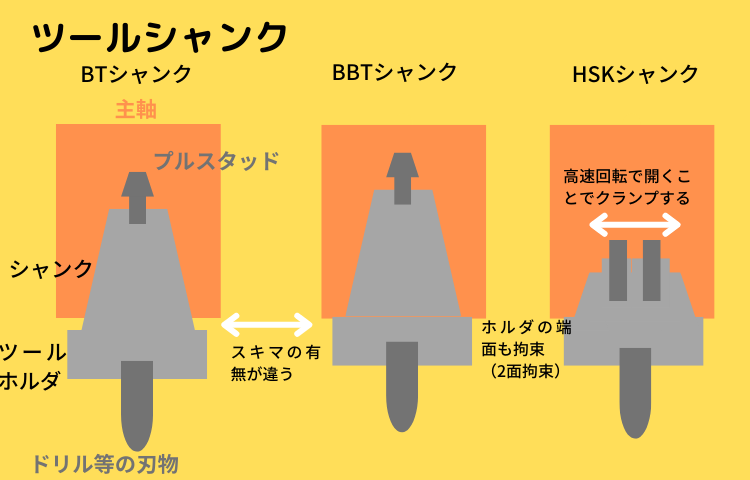
※日本では一般的にBTシャンクがよく使われています。そのためマシニングセンタの主軸のサイズの違いで”30番””40番”などと言われます。
(マシニングセンタにおいて)○○角
テーブルの大きさ。400角であれば400mm x 400mmのテーブル。400,500,630,800など。
ATC(オートツールチェンジャー)
工具を自動で交換する装置。この機能があるため、自動で複数の加工を連続して行うことができる。その点がマシニングセンタとNCフライス盤の大きな違い。NCフライス盤には基本的にATCがないため、一度加工して、工具を取り替え、芯出しが必要となる。タレットの周囲に工具がついていてタレットが回転して工具交換をするタイプ(タレット式)と、チェンジアームがマガジンから工具を交換するタイプがある。
ブラザー工業製のマシニングセンタのツール交換やマガジンがわかる動画はこちら。
ATCマガジン ATCするために保管する工具のマガジン。
マトリックスマガジン ATCマガジンの一種。直行座標で工具を収納するマガジン。一般的に100本以上の工具を使う機械に使われるため長時間の自動化や多品種むき。
メモリーランダム方式 工具交換の方式。アームの工具交換動作が1回で済む。マガジンと工具の場所を記憶している。
ゲージライン ATCにおいてチェンジアームと主軸スピンドル、またマガジン側のツールホルダのゲージラインでチェンジアームの調整をする。
Tool to Tool 工具交換の時間を表す。マガジンと主軸が工具を交換する時間。
Chip to Chip 切削を止めてから工具を交換して次の切削を開始するまでの時間。
APC(オートパレットチェンジャー)
マシニングセンタのパレットを自動で交換する装置。横型マシニングセンタに多い。2面APCの場合、1面で加工中に、反対側のパレットでワークセットなどの段取り替えができるため、機械が止まる時間を減らせる。2面だけでなく、より多くのパレットを自動で交換することで夜間などの長時間の自動運転が可能となる。
DMG森精機の多面パレットチェンジシステム
エッジロケーター
パレットの位置きめをする板。APCでパレットチェンジをした時に、エッジロケーターを当てることで位置を確認。そうすることで自動加工を実現できる。なかった場合、パレットチェンジの度に(パレットの位置を確認するため)芯出しが必要となる。
イケール
ワークを取り付ける治具の一種。90度を正確に測るための台。ボルト穴が空いておりクランプをボルト止めしてワークをクランプして止める。2面使用する2面イケールや4面使用できる4面イケールなどがある。
オートカプラ
エアや油圧、クーラントなどの配管を接続する継手・コネクターを自動で接続・離脱できるもの。離脱しても外部に流体が漏れない仕組みになっているため、工作機械の自動化、パレットチェンジャーの油圧配管などに用いられる。
マシニングセンタに取り付けられる機器・オプション
チップコンベア
切粉を回収して、機外に排出するコンベア。切粉の形状や材質に合わせて様々なタイプがある。
チップコンベアに関してもモノタロウにわかりやすい解説がありましたのでリンクを貼らせていただきます。
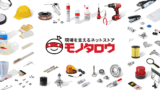
クーラントタンク
クーラントを入れておくタンク。ここからポンプで吸い上げてクーラントをかける。かけられたクーラントは切粉と一緒にチップコンベアへ送られる。チップコンベアはクーラントタンクと繋がっている。一度使用したクーラントは一度フィルタなどにかけられて切粉をとってから再利用される。
サイクロンフィルタ 遠心分離式のフィルタ。使用済クーラントを遠心分離させることで切粉などのゴミを除去する。
マグネットセパレーター 細かな切粉を除去するための装置。磁力で金属の粉を吸い取る。
フロートスイッチ:液面に浮かべたフロート(浮き)が浮力で液位に合わせて上下してON/OFFを切り替えるレベルスイッチ。
クーラント
切削油。切削する時に加工点を冷却したり、切粉を除去したりするためにかける油。水に希釈する水溶性と、油性がある。油性は沸点が高いためより高温化での加工が可能だが、火災の危険がある。マシニングセンタでは主に水溶性クーラントが用いられれる。
MQL:セミドライ加工。少量のクーラントを加工点に塗布して金属などの加工を行うこと。
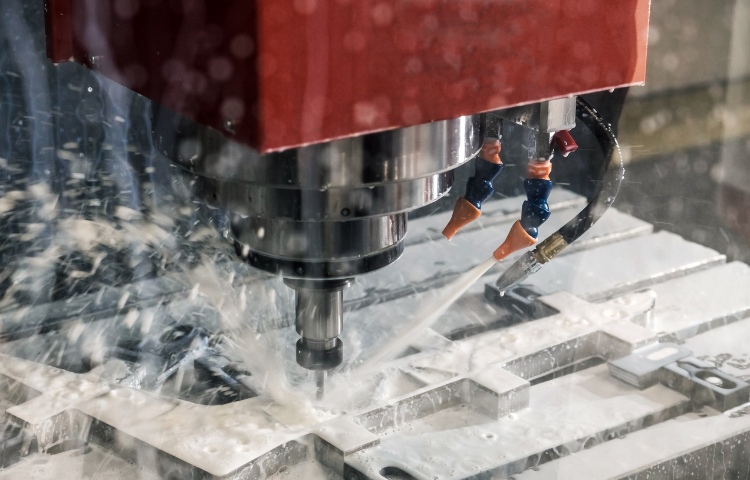
シグナルタワー
機械の状態を表す、機械上部に設置されたライト。パトライト社が有名で、パトライトとも呼ばれることが多い。
リニアスケール(リニアエンコーダ)
ものさしと検出器(目盛から位置情報を取得するもの)から構成される直線上の位置や距離を測定する機器。工作機械などではある物の実際の位置や移動量を測定して把握することに用いられれる。電磁式と光学式がある。
スケールフィードバック
テーブルなどの送り軸と平行に取り付けたスケール(物差し)により位置を検出して補正する機能。熱の影響や、摩耗などによりNC制御した位置に実際には正確に移動しない場合があるので、直接位置を検出して補正するために取り付けられる。XYZの軸ごとに取り付け可能で、重要な軸のみに取り付けることもある。
タッチセンサ
工具やワークに触れて、寸法や位置を計測する機器。工作機械においては、工具に触れることで工具の長さ、径などを測ったり、ワークに触れて寸法や位置を測ったりするために使われる。通電式と内部接点方式、レーザー方式がある。
接触する部分をタッチプローブと呼ぶ。
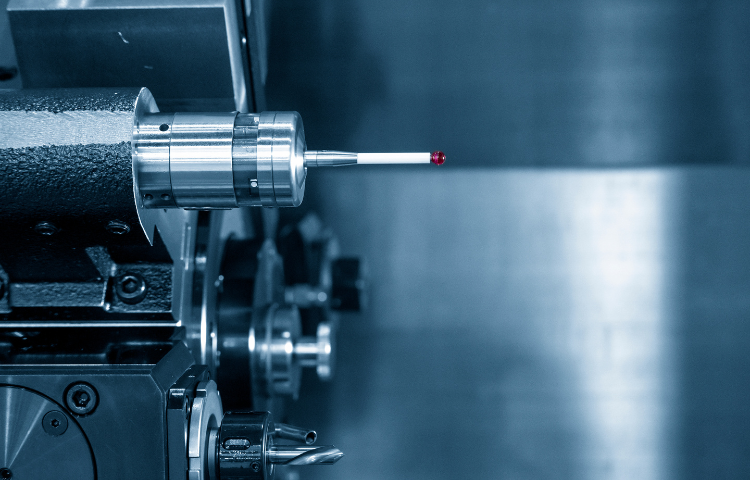
ツールセッター(工具折損検知)
工作機械におけるツール(工具)用のタッチセンサ。工具長を測定することなどに用いられる。
加工前に工具が折れていないかを確認する工具折損検知装置としても用いられる。工具折損検知装置はツールマガジン内に設置するタイプと機械内に設置するタイプがある。機械内に設置する場合、加工中などは切粉などで破損しないようカバーなどに隠れている場合が一般的。
ワークセッター
工作機械におけるワーク用のタッチセンサ。ワークのどこか三点をタッチして計測することでワークの3次元の位置、寸法を把握することができる。例えば、加工前にワークセッターでワークに触れることで、ワークの位置のズレを確認。実際のワークの基準から、プログラムを開始することでワークのずれによる加工誤差をなくす。機械のオプションとしては、自動計測機能や機内計測装置などという名称。
オイルスキマー
浮上油回収装置。ベルト式では、ベルトで液面に浮いた油を回収して、スクレーパでとる。汚れた油を撮ることでクーラントの腐敗や悪臭を防ぐ。
オイルミストコレクタ
工作機械から発生するオイルミストや溶接現場でのヒューム、ポンプの排気中の油分を補修し、快適な作業環境を確保するための装置。捕集方法は、フィルター式(フィルタ交換が必要)、遠心分離式、電気集塵方式がある。
エリアセンサ・ライトカーテン
あるエリアに手や物が入ったことを検知するセンサ。通常は光線式で、遮られるとすぐに検知でき、機械を停止させる。加工中に人の手が入ってしまわないように扉などに設けられる。機械内以外でも駆動コンベアなど自動で動いて人の手が挟まれたりする危険がある場所には設置される。
電磁ロック
扉などに取り付けられるロック。これが外されると機械の電源が入らなくなる。メンテナンスなどで扉を開けて作業する場合、機械が駆動しないようにする。
インターロック
ある一定の条件が整わないと動作が開始しないようにする制御の安全機能。例えば、扉を閉めたことを確認しないと機械稼働ができないなど。
着座確認
ワークや治具などがその場にあるかを確認する機能・センサ。一般的にはエア配管を通したセンサで、ワークなどが置かれるとエアが詰まるため、ワークがあることを認識できるような機能が多い。しっかりワークや治具がセットされないまま機械を動かして事故につながる危険を防ぐために用いられる。
センタースルークーラント
加工の際に工具の中から出すクーラントのこと。切粉の除去や加工点の冷却の効果があり、長穴を加工する場合にはよく用いられる。センタースルークーラントを出す主軸をスルースピンドルという。
ステップ・ノンステップ加工:長穴などを加工する際、切粉を除去するために少し削って、少し戻ってを繰り返すことをステップという。それがなく、一発で加工することをノンステップという。
漏電遮断器
漏電による感電事故や火災が発生する前に電路を遮断する装置。
軸芯冷却
回転する主軸の内部に温度制御した多量の冷却油を送り込み、主軸自体を内側から冷却する方式。
ボールねじ軸芯冷却 サポートベアリングにも冷却油が潤滑するタイプのボールねじ。
オイルクーラー(チラー、オイルコンディショナ)
主軸の冷却油などを冷やすクーラー。冷却油が熱を持ってしまうと、主軸など駆動部の熱を下げることができず、加工精度に影響が出る。そのため冷却油の温度管理をすることで、長時間の加工精度を安定させる。
自動消火装置
油性クーラントの使用などによって機械内で火災が発生した場合に消火する装置。熱や炎など、様々な方法で検知する。
防火ダンパ 羽根状の扉や板状の扉。火災時に温度が上がると、ダンパーについているヒューズが溶解して、ダンパーがさがり、炎や煙を遮断する。
操作盤・NC装置の機能やオプション
補正
加工や位置精度などの制御している狙い値と実際に測定した位置のズレを計算で直すこと。加工したものを測定して、ズレがあれば、その数値分加工をすること。実際にズレる量を計算して、プログラムを自動で変更する機能。補正することを「補正を入れる」という。
工具補正
長さや径など工具毎に異なる寸法を自動で計算して、同じ座標を入力することで加工できる機能。工具の情報を入力することで、加工プログラム作成時には同じ座標で問題なくできる。この機能がなければ、同じ座標を入力しても工具毎に刃の位置が異なり、寸法が狂ってしまう。
リミットスイッチ
機械検出をアクチュエーターを介して動作させる電気スイッチ。動力機械のストローク極限のための自動停止や、位置検出に利用される。筐体は金属や樹脂製のケースにして、スイッチ保護することで耐環境製を持たせている。
工作機械では、例えばある位置にワークや機械の駆動部品がきたことを確認するために用いられる。リミットスイッチがONしたことを確認して次の動作に移る制御にすることで、ポカヨケや干渉を防ぐことができる。
パルスハンドル
NCコントローラーなどについているグルグル回す目盛付きのハンドル。これを操作することで、手動操作時に主軸などを動かすことができる。
Gコード
加工を行うための準備機能。00~99まで位置決めや補正などさまざまな機能を有したコードがある。
Mコード
加工を行うための補助機能。機械に様々な補助動作を行わせる指令。マシニングセンタではほぼ使われる。
ヘリカル補間
NCプログラムの指令の1つ。指令された送り速度で指示された位置まで螺旋状に移動する。
カスタムマクロ
メインのプログラムとは別にプログラムを記述して同じプログラムを寸法の違う様々な製品に使い回す機能。
同期タップ加工
NCによって主軸の回転と送りを同期させ、ねじを加工する方法。
固定サイクル
よく使われる加工サイクルを1つのブロックとして指令できる機能。G○○で表される。
リジットタップ・同期タップ・シンクロタップ
タップ加工をする際、主軸の回転と送りを同期させて加工する方法。高精度なタップ加工ができる。専用のツールがある。
原点
機械の駆動する部分の初めの位置。異常停止した後には一度原点に戻らないと再起動できないようになっていたり、プログラムを作る際の初めの位置として利用したりされる。
原点復帰 異常停止などの後、原点にもどること、そのための機能。
その他のよく使われる用語
ビルトインモーター
機構装置・部品に内蔵されたモーター。装置設計、性能の最適化が可能。例えば旋盤の工具主軸と一体となったモーター。高速回転ができるが、モーターの熱が主軸にそのまま伝わる。
アンカー(ボルト)
機械などを床に据付て固定するためのコンクリート基礎に埋め込むボルト。
インターフェース(工作機械において)
言葉の意味は界面や接触面、中間面といった意味。コンピューターと周辺機器の接続部分。工作機械においては、機械本体と何か周辺機器の接続部分のこと。何か付帯設備やPCなどを接続する場合、インターフェースの形状を合わせておく必要がある。
ユーザーインターフェース
人間と自動機械との間の複雑な操作をする手順。規則との意味としても使われる。
リニアモーター
軸のない電気モータのこと。直線運動をする。通常のモーターは回転運動をする。その回転運動をするモーターを伸ばしたもの。
アンダーレース潤滑
ベアリングの潤滑は、主軸内側に送り込んだ冷却油をベアリングのインナーレースに開けた穴から供給する。
まんじゅう(嵩上げ)
機械の高さを上げるために下にしく土台。ユーザーのライン高さに合わせるために用いられる。
以上、1年目にマシニングセンタの打合せや見積でわからなかった単語の意味を紹介しました。この記事があれば、見積内の単語の意味は理解できるのではないかと思います。具体的な部分は別に詳細記事で紹介していきたいです。