生産性が上がると考えられているサーボプレス!!ではどのような加工や製品で生産性が上がるのでしょうか?今回はサーボプレスの機能を活かして、生産性を向上できる加工事例や方法を紹介したいと思います。
※サーボプレスの構造やメカプレス・油圧プレスとの違いに関しては以下の記事で解説しています。
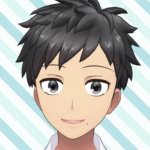
こちらの記事の中で、サーボプレスの大きな特長は、1.位置制御、2.速度制御、3.圧力制御ができること、それらを組み合わせた独自の動き(フリーモーション)ができることと紹介しました。その特長を活かした生産性向上案を紹介します!!
深絞り加工
サーボプレスでは深絞り加工が可能です。低速で高トルクの加圧、及び加圧を続けることができるため深絞り加工(コップのような形状の成形加工、板に加圧することで金型のパンチ形状に沿って下に伸ばすイメージ)ができます。メカプレスは同じ速度で下降し、下死点でしか最大加圧力を出せないため、加圧すると製品が破れてしまい深絞り加工には向いていませんでした。逆に速度を落とすと、加圧しない部分の動きも遅くなるので生産性が落ちていました。
またメカプレスで行う場合は同じ速度で1回転(1度の下降上昇のサイクル)行うため、何工程かに分けて絞り加工を行う場合、工程・金型を分けなければいけません。その点、サーボプレスは速度や圧力を変えながら、一つの金型で何工程かを行うことができるので、コスト削減に繋がります。
加圧し続けて金属を伸ばして成形する必要があるという点で深絞り加工では油圧プレスが使われることが多いです。油圧プレスと比較したサーボプレスの利点は以下の3点です。
1. 加圧しない部分の動きを早くすることができる。
2. 位置制御・圧力制御によりより詳細に工程を設計できる(例えば少し加圧して一時停止してから再度加圧などを数値で設定ができる)
3. 油漏れや油交換の必要がないためメンテナンス性が良いという点があげられます。
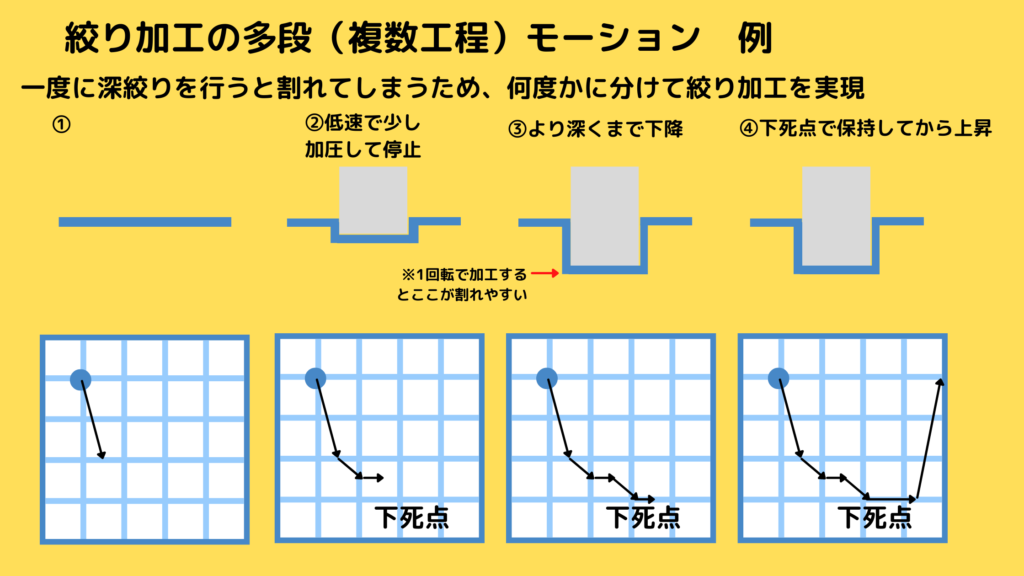
反転モーションによる半抜き加工
スライド位置を精密に制御して下死点に行く直前でプレスの回転を反転させる工法です。(モーションに関しては下記記載)これにより半抜き加工などが可能です。
※半抜き加工とは、成形を開始してから抜ききるまでに加圧をやめることで、絞り加工を行う加工法です。抜き切らずに模様をつけたりする製品に利用されます。
事例:電子部品のケースへのエンボス加工、缶詰のプルタブ
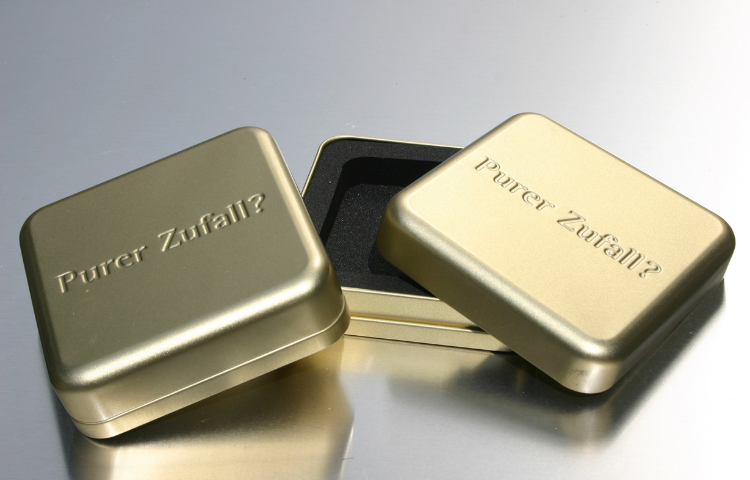
高精度な曲げ加工
フリーモーションにより、加圧時だけ速度を落として加工、及び下死点での加圧しながら保持することなどができるため、曲げ加工を高精度に行うことができます。通常曲げ加工はスプリングバックと呼ばれる曲げた部分が元の形(平な形)に戻ろうとする現象が起こります。メカプレスで1回転で加工する場合は、スプリングバックの影響を受けてしまい、高精度な成形ができません。またスプリングバックを抑えるため低速にすると、加圧しない部分も低速になるため生産性が上がりません。
後工程でカシメや組立など、他の部品と交わるために高精度が必要な部品の曲げ加工などにはサーボプレスが最適です。
プレスブレーキでの曲げ加工も含まれますが、曲げ加工やスプリングバックに関しては下記記事に詳しく書かれていました。
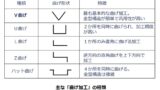
振子モーションによる高速加工
サーボプレスの構造の記事で解説しましたが、振子モーションで加工することにより生産速度を大幅に上げ、生産性を向上することができます。
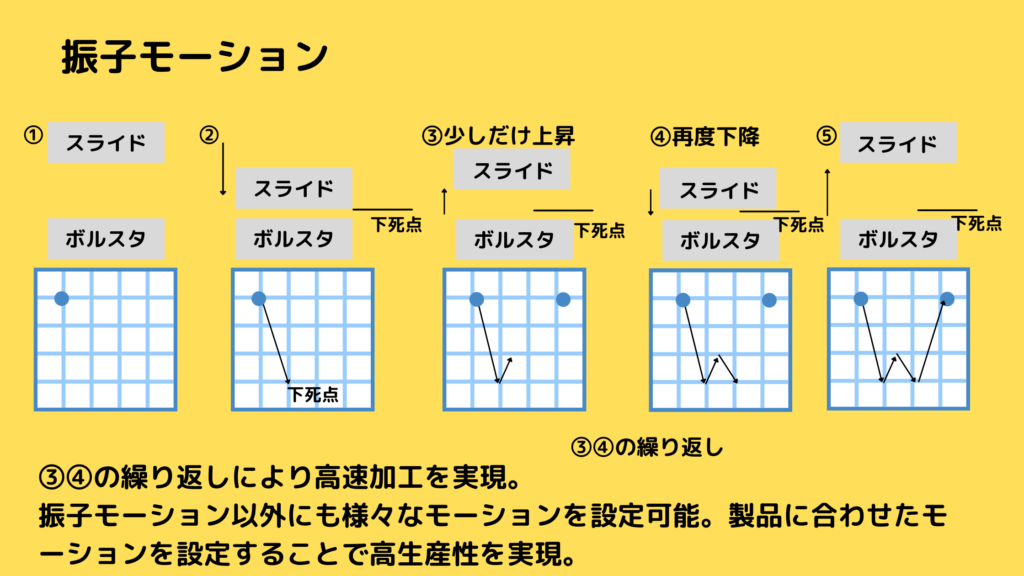
実際の事例:
長尺材の建材において、プレスの穴空け工程→曲げ工程で完成する製品がました。プレスの穴数が多くプレス工程がネックとなり、曲げ工程はスピードを落として生産していました。そこで110tのサーボプレスを導入、振子モーションにて高速の穴空け加工を行うことで、今まで約70spmで生産していたところ約2倍の130spmでの生産が可能となりました。サーボプレスの初期費用は、メカプレスと比較して4,500千円程嵩みましたが、好景気も重なり2年目から元は取れたのではないかと言って頂きました。
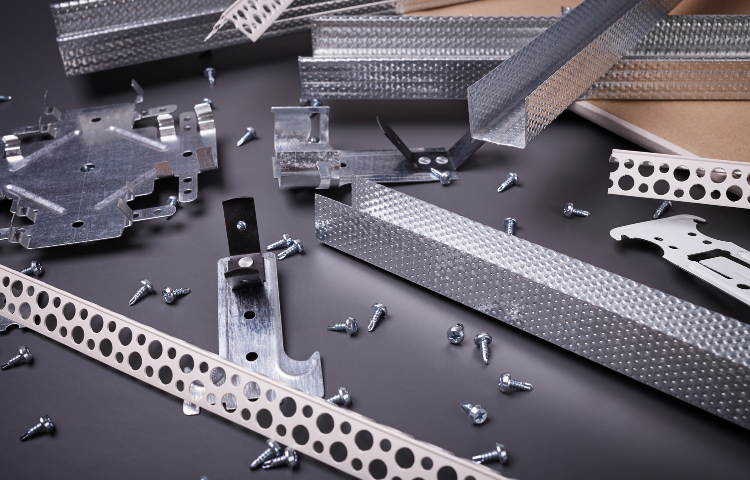
数値管理による品質の向上・品質管理
スライド位置管理による高精度加工の実現
スライド(上型のつく板)の下死点位置を制御、自動補正(自動で修正)できるため、連続運転時の熱膨張に対しても寸法安定、不良率の削減に繋がり、高精度加工を実現させます。連続運転時におけるダイハイトの微調整が不要となります。
実際の事例:
精密な成形が必要なモーターコアの部品において、メカプレスで実施していた時は作業者による下死点管理が必要でした。抜き打ちで点検を行い、微調整が必要な際は数十分機械を停止する必要がありました。サーボプレスにすることで自動補正により生産中の微調整回数を無くしたこと、またその機能があることで成形品の納品先からも品質管理の信頼を上げることができました。

荷重管理によるトレーサビリティの実現
サーボプレスは荷重(加圧力)を数値で設定できますが、実際にかかっている荷重をロードセル(荷重計)で計測することもできます。計測した数値に対して狙い値を微修正できるため、連続運転時の金型の熱膨張による変化などに自動で対応ができます。
荷重を数値管理することで、トレーサビリティ管理を行うことができます。
トレーサビリティとは、「その製品がいつ、どこで、だれによって作られたのか」を明らかにすべく、原材料の調達から生産、そして消費または廃棄まで追跡可能な状態にすることです。
キーエンスHP keyence.co.jp 「トレーサビリティ大学」
上記だけでなく、自動車や航空機部品など高品質が求められる製品は、何かトラブルが起きた際に、その生産段階の検査結果などまで追跡することがあります。荷重を数値管理することでプレス工程での製品品質を保証することができるため、トレーサビリティの観点からサーボプレスを導入される企業も多いです。
実際の事例:
高度な品質管理・保証が求められる航空機部品の深絞り、圧入に関して実際にどのくらいの荷重がかかっているかをデータ管理する必要がありました。今まで油圧プレスで深絞り加工を行い、データ管理はできていませんでしたが、サーボプレス化することで、荷重と位置の関係をワークごとに記録、トレーサビリティ管理することができ、新たな航空機部品の受注につながりました。
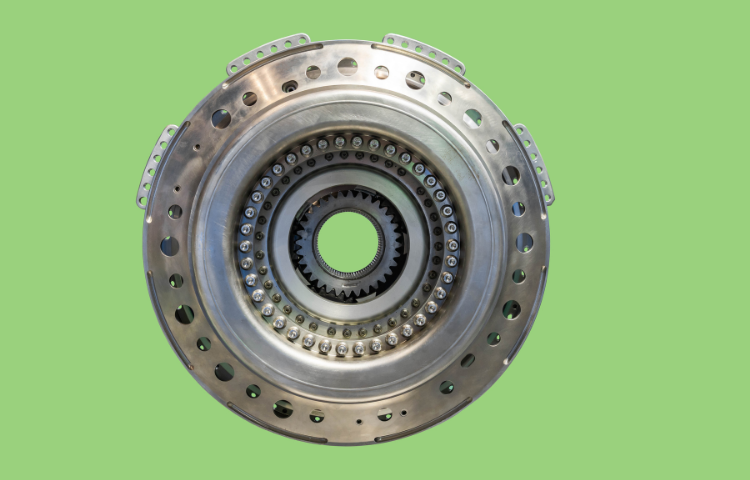
金型寿命の向上
速度を変更できるサーボプレスでは、金型に当たる寸前で下降速度を減速して成形することで金型へのダメージを減らし、金型寿命を伸ばすことができます。速度を常に監視してコントロールできるため、加圧時の速度も(自動補正を行い)一定に保つことができます。
実際の事例:
抜き加工を行っているプレス工程において、金型寿命を約7倍にした例や、ダメージを軽減することで金型自体の材質を低価格なものに変更できた事例などがあります。
環境改善・省エネ
環境改善する手段としても利用されています。油圧プレスでは、油漏れが起こってしまったり、油圧ポンプ自体が発熱するので工場環境も悪化します。さらに常に電気を消費していることになります。サーボプレスにすることでそのようなリスクやコストを削減できます。また、加圧時だけ低速にすることで、プレス音も減少させることができ、工場環境の改善にもつながります。
実際の事例:
昔からの工業団地でも昨今住宅が立ち並んできて、プレス音に対する苦情が増えています。先に工場があったにも関わらず不利な状況になってしまう場合も多々あります。近くに引っ越してきた人の苦情で困っていたプレス屋さんも次に更新するプレスからサーボプレスにすることで騒音を対策するようになったこともありました。
以上、サーボプレスが実際に使われている加工事例や生産性向上事例を6パターン紹介しました。フリーモーションができることが一番の特徴なため、もちろん他の加工でも使われていて可能性は無限大です。何かサーボプレスの検討に少しでもお役に立てれれば嬉しいです。