こんにちは。以前無人搬送車(AGV)でできる搬送工程の自動化事例を紹介しました。今回はAGV以外の事例を紹介します。実際には、生産工場でAGVがしようされている例はまだまだ限られているので、本記事のロボットやガントリーローダーを利用した工程間搬送の自動化の方が実用されています。
搬送工程の種類
そもそも工場内の搬送工程には、大きく2つに分けられると思います。次の1.の「工場内のライン間、建屋間、エリア間などの搬送」の自動化はAGVで行うのが適切です。今回は2.の「生産工程間、ライン内機械間の搬送」の自動化方法を紹介したいと思います。
1. 工場内のライン間、建屋間、エリア間などの搬送
各ラインと次のラインのとの間、工場のある場所から別の建屋に持っていく場合や、生産ラインから測定室や出荷場に持って行ったりといった通路などを超えてモノを運ぶパターンです。
搬送距離が長く通路を越えるため、運ぶ機械が常時通路を塞いでいるわけにはいきません。さらに人やフォークリフトなどとぶつかる可能性があるため、フレキシブルな搬送機械・方法が必要になります。
実際は、人がハンドリフトや台車を押して運んだり、フォークリフトで運んでいる場合が多いです。下記記事で事例を紹介していますが、この場合は常時通路を塞ぐことがないAGVが適切です。
2. 生産工程間、ライン内機械間の搬送
前工程から次工程までの各生産工程の間や、機械と機械の間を搬送するパターンです。機械の間は普段は作業者が入らないよう区切ることも可能なため、自動化がしやすい部分になります。しかしそれぞれの治具で位置決めをしなければならないことも多く、ワークを位置決めピンに差し込んだり、ズレないような工夫をしたりといった、より精密な搬送が必要となります。
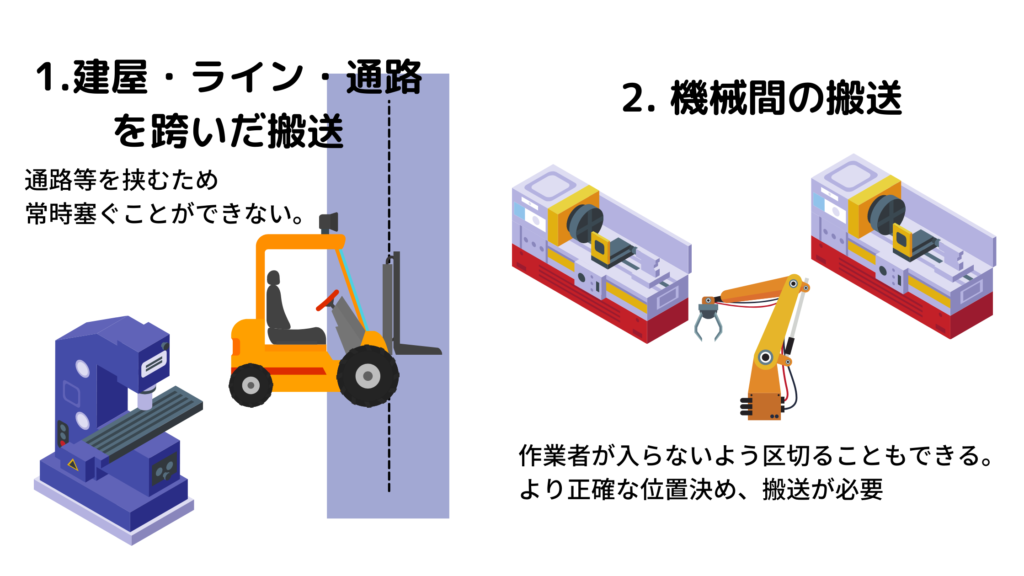
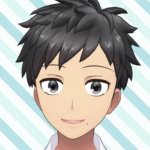
今回はこの「2.生産工程間、ライン内機械間の搬送」を自動化する方法を紹介します。
搬送方法の選び方・おすすめの自動化方法
紹介する方法もそれぞれ向いている製品が様々です。各方法の紹介の前に、製品や要望によってどの方法が向いているかを簡単に次の表にまとめてみました。
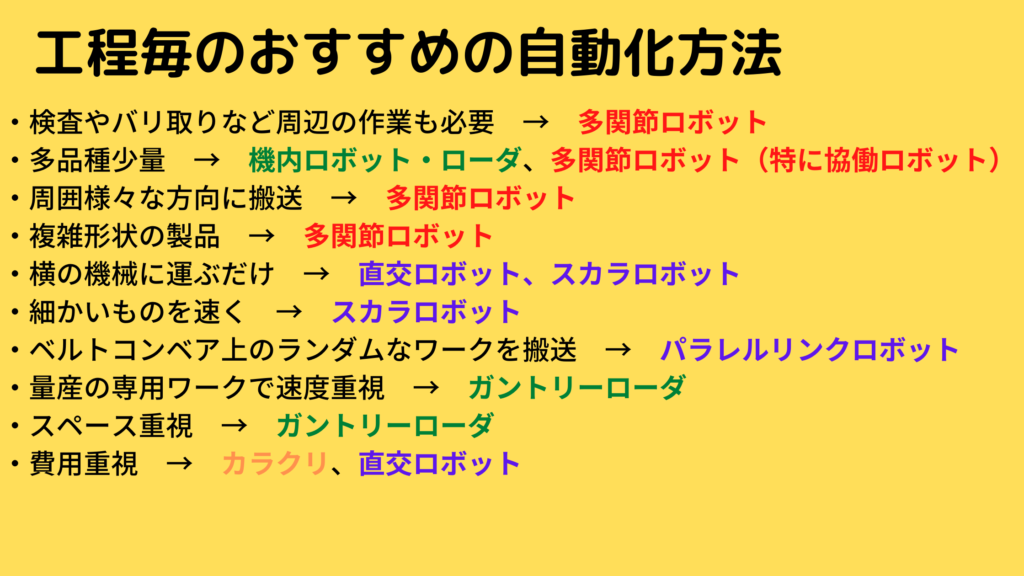
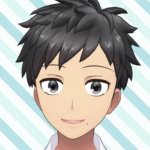
それではそれぞれの特徴を見ていきましょう!!
多関節ロボット
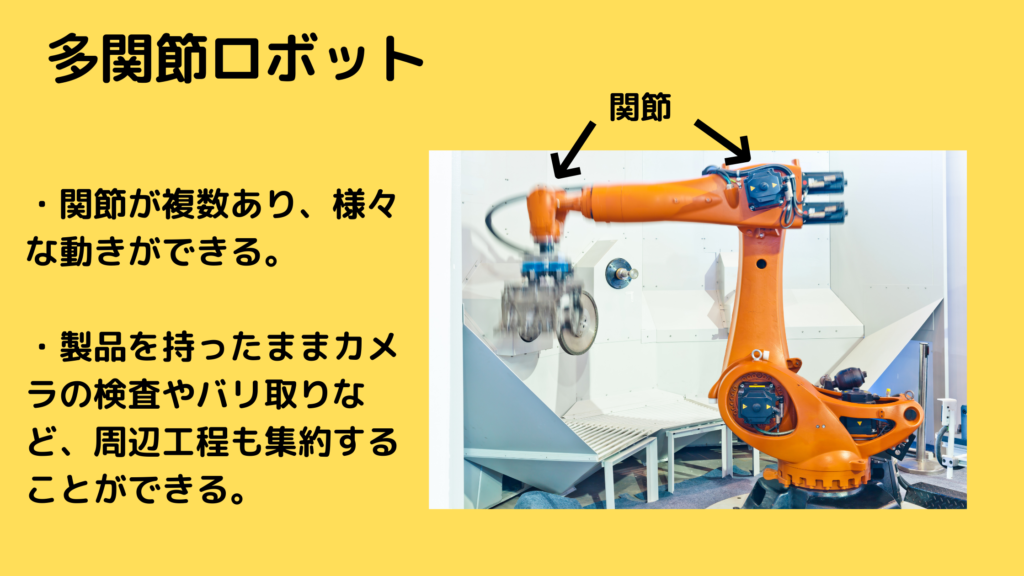
多関節ロボットは人間の腕のような形状をしており、回転する軸(関節)を複数持ったロボットのことです。複数の関節を利用して様々な向き、角度に動かすことができます。腕が1本のものが主流ですが、より人間に近い2本の腕を持って同時に制御できる双腕型もあります。
稼働範囲に人が入らないよう安全柵を設ける必要があり、リーチ内(ハンドが届く範囲)でしかものを運ぶことができませんが、軸が多く自由な動きができるため複雑な形状の製品を搬送できます。さらにバリ取りや測定、検査など周辺の工程と合わせて自動化ができることも魅力の一つです。
多関節ロボットの中でも人との共存できることを目的とした協働ロボットは、安全柵が要らず省スペース化することができ、動作のプログラミング(ティーチング)も通常のロボットと比較して簡単にできます。移設・ティーチングが簡単にできるため、多品種少量の製品にも向いています。
メリット
・動きの自由度が高い。様々な向き、角度に動かし複雑な動作ができる。
・周囲360度に搬送が可能。
・他工程の追加も可能。(運ぶ途中で製品を持ったまま検査カメラで撮影させる等)
・協働ロボットの場合、移設、ティーチングが簡単。
デメリット
・設置スペースが必要。
・リーチが届く範囲でなければ搬送ができない。
・動きをプログラミングしてシステムにする業者や作業が必要。
・速度はロボットの速度になる。(ローダーの方が速い)
☆事例☆
他のロボット(直交・スカラ・パラレルリンクロボット)
多関節以外のロボットで運ぶこともできます。軸(関節)や動きが絞られているため、比較的動きが速く、搬送時間を削減する目的で使用されます。
直交ロボット
直線的な動きをする軸を1~3軸程、交差させて動くロボットです。様々な軸を組み合わせることで様々な動きが可能です。1つの機械内で使われることも多いです。
射出成形機では取出機と呼ばれる、成形機から製品を取り出して外に置く動きをする直交ロボットでの自動化が一般的です。
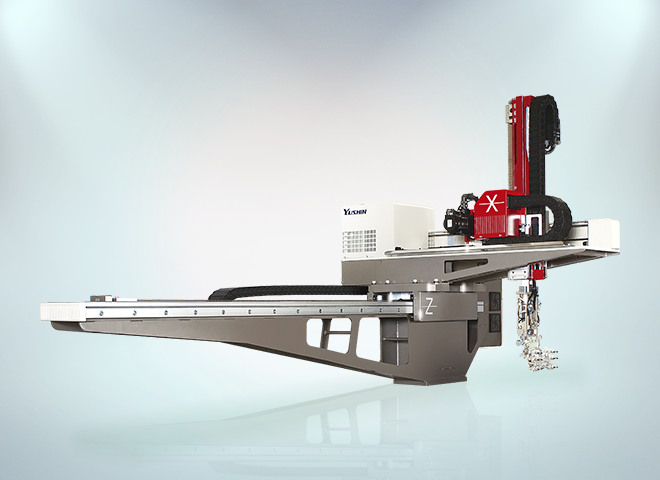
メリット
・シンプルな構造。壊れにくく比較的低価格。
・組み合わせが可能。機械内でも使用される。
・直線的な動きのみのため動きが速い。
デメリット
・複雑な動きができない。
・多関節と比べて動かす部分全体にロボットの土台(レール)があるため、比較的サイズが大きい。(反面丈夫に設置もできる)。
スカラロボット
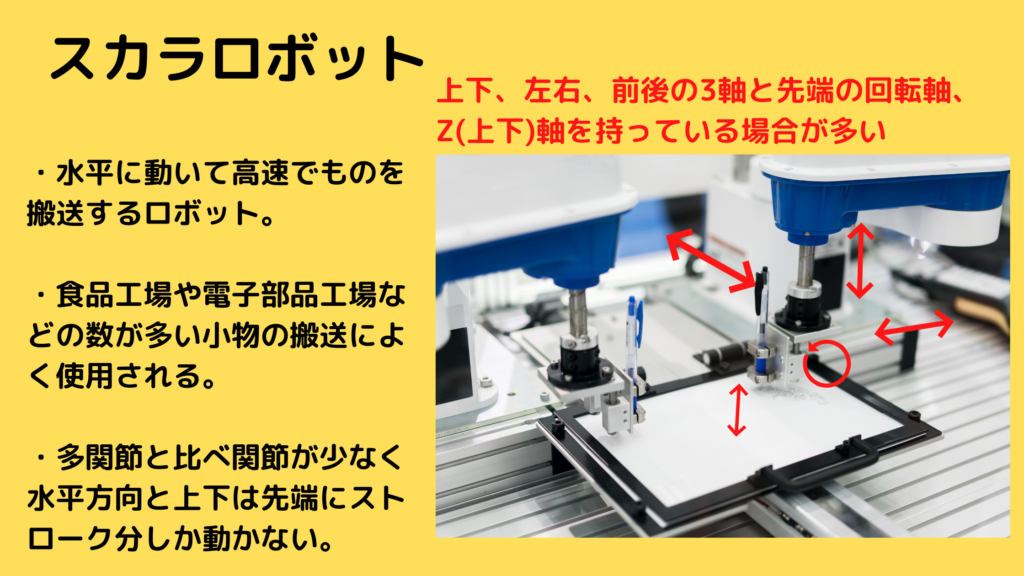
水平多関節ロボットとも呼ばれ、水平にモノを運ぶことに適しています。一般的に上下、左右、前後の他、先端にZ軸、回転軸を持っているタイプが多いです。コンベアから製品をとってすぐ横に運んだり、基盤を組立たり、部品を整列させたりといった工程に使用されます。流れてくる製品を吸盤やハンドでとって、箱に詰めたりする食品工場等でよく使用されています。
メリット
・シンプルな構造。壊れにくく比較的低価格。
・背も低く無駄な軸もないため動きが速い。
デメリット
・水平にしか搬送することができない。
・リーチが短い。
・スペースが必要
パラレルリンクロボット
複数のモーターとリンク機構でアームを動かす速度を上げることに特化したロボットです。流れてくる製品をとって、箱詰めすることによく使用されます。主に上部から製品を吸着して、横に運びます。
メリット
・パラレルリンク機構で動きが速い。
・上部に設置できるため、スペースをあまり取らない。
デメリット
・位置制御ができない。
・取る製品を確認するためにカメラが必要。
ガントリーローダー
自動車のエンジン部品加工ライン等、金属加工の量産ラインでは設備上部にローダーを設置して搬送するガントリーローダーが使用されています。機械を何台も並べて、一台のガントリーローダーで搬送します。ストッカーから取り出して、各工程の設備を周り、完成品ストッカーに入れるまで全工程一貫して自動化を行うことも可能です。特に旋盤では、各設備メーカーがガントリーローダーもセットで製作する場合も多いです。
メリット
・剛性が高く、スピードが速い。
・連結して設置できるため、複数台の機械を自動化できる。
・上部に設置できるため省スペース
・周辺装置(ストッカーや検査機、洗浄機等)と組み合わせてシステム化できるところも多い。
デメリット
・基本的に取り外しはできないため専用機となってしまう。(ハンドの脱着は可能)
・複雑な向きで製品を掴むことが難しい。
・ライン構成が直線的になってしまう。
ガントリーローダー量産ライン例
機内(内臓型)ローダー・ロボット
マシニングセンタや旋盤の中に埋め込まれたローダーやロボットで運ぶ方法です。昨今の自動化・省スペースのニーズから、設備メーカーがオプションで用意していることも多いです。機内にあるため、省スペースで機械と同一の操作盤で制御できることが強みです。
メリット
・機内のためコンパクトで省スペース。
・機械側の制御と統一できる。
・使いたい時だけ使用できる。
デメリット
・機内のスペースが減る。
・リーチが短い。(マシニングセンタなどで複数台連結する場合は機内ローダーありきの機械しかできないことが多い)
参考商品 オークマ製旋盤内臓ロボット
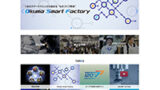
シューター、フリーローラーコンベア、カラクリ
今まで紹介したものは全て自動化するために高額な設備投資をしなければなりません。安くて100万、多関節ロボットやガントリーローダの場合1,000万円を越えることも多いです。そこで動力を使わずに、シューターなどメカのカラクリを利用すると安価に自動化が可能です。工程間が狭かったり、機械内で搬送する場合は、まずはカラクリで自動化ができないかを考えてみてから設備投資を考えるのも一つの手かもしれません。
シューターやフリーローラーコンベアは、その上をワークを単純に滑らせるだけでは傷がついてしまいます。そのため、傷がつかないように、ストッパーを設けたり、徐々に減速させたりするカラクリを作ることで、電力などを利用しない自動搬送が可能となります。
特にトヨタ関連の工場では細かい部分でカラクリのノウハウが多数利用されています。
メリット
・安価。費用対効果が高い。
・設備を追加するわけではないため、無駄なスペースを取らない。
デメリット
・大掛かりなことはできない。
・電気制御がないため安全管理が重要。
・設計、検証に時間がかかる。
以上、如何でしたでしょうか。搬送の自動化といっても様々な方法があり、自社の製品やラインにあった形のものを探して導入しなければいけません。搬送を自動化する際の少しでも参考になっていれば幸いです。